Industrial line
Our wide range of industrial gasketed plate heat exchangers is suitable for all types of industry and multiple applications from heating, cooling and heat recovery to condensation and evaporation. We are constantly looking to extend and upgrade the range, adding new performance criteria and greater flexibility. What’s termed ‘next-generation’ today will soon be standard for the entire Alfa Laval Industrial line.
Towards new standards in efficiency, reliability and serviceability
- High energy efficiency
- Flexible – configurable for broad range of applications
- Ensures optimal performance in specific applications based on specific needs
- Easy to install
- High serviceability
Demand new standards
Introducing the world’s most modern Gasketed plate heat exchangers. Discover how our next-generation line of gasketed plate heat exchangers will bring you higher efficiency, better reliability and greater serviceability.
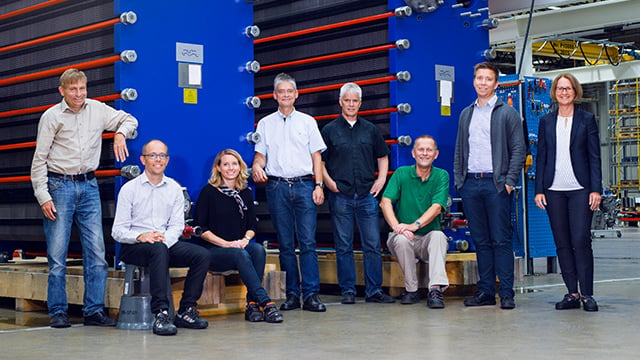
How it works
The heat transfer area of a gasketed plate heat exchanger consists of a series of corrugated plates, assembled between a frame and pressure plates to retain pressure. Gaskets act as seals between the plates. Fluids normally run counter-currently through the heat exchanger. This gives the most efficient thermal performance and enables a very close temperature approach, ie the temperature difference between the exiting process medium and the entering service medium.
Alfa Laval liquid/liquid gasketed plate-and-frame heat exchanger
Alfa Laval steam heater gasketed plate-and-frame heat exchanger
Alfa Laval 2-pass gasketed plate-and-frame heat exchanger
Features that make the difference
The Industrial line is equipped with features that turn this high-performance family into efficient and reliable workhorses that are easy to service and maintain over the whole product lifecycle.
For efficiency
By improving the efficiency of your heat exchanger, you can maximize production and minimize energy consumption to reduce your power bill and improve your environmental footprint.
See product animations below or get more information and listen to our technical experts.
CurveFlow™
distribution area
Improves media flow and minimizes risk of fouling.
Offset gasket groove
Ensures plate utilization for maximum heat transfer efficiency.
OmegaPort™
noncircular port holes
Enhances media flow and thermal efficiency.
FlexFlow™
plate design
Improves thermal efficiency and optimizes pressure drop utilization.
For reliability
We are always looking to increase the reliability of every aspect of our gasketed plate heat exchangers. We focus on durable designs based on robust materials and safe manufacturing processes.
See product animations below or get more information and listen to our technical experts.
PowerArc™
plate pattern divider
Improves plate rigidity for longer lifetime.
Five-point alignment
Ensures reliable plate positioning and easy to service for large units.
SteerLock™
plate alignment
Ensures reliable plate positioning and easy service.
For serviceability
The simple opening and closing of the plate-and-frame design with gaskets enables hassle-free inspection and service. It also enables you to easily adapt the unit to new process conditions.
See product animations below or get more information and listen to our technical experts.
ClipGrip™
gasket attachment
Ensures perfect seal and trouble-free maintenance.
T-bar roller
Provides a lower unit that is easy to service.
Bearing boxes
Guarantees an easy-to-open unit for smoother, more efficient maintenance.
Compact frame
Facilitates maintenance and minimizes service area requirement.
Discover more features
There are many more features in an Alfa Laval gasketed heat exchanger that make a difference. New innovations and proven concepts together offer extensive benefits such as low total product life cycle cost, increased production output, minimized downtime and increased staff safety.
See the product leaflets to find the full list of features of each model in the Industrial range.
Corner guiding
Tilted bolt opening
Leak chamber
Elongated nuts
Lock washer
Fixed bolt head
Key hole bolt opening
Pressure plate roller
Different plates for different industrial needs
Plates are available with various pressing depths, angles of chevron pattern and various corrugation shapes, which are all carefully designed and selected to achieve optimal performance. Our Industrial line is available with four main plate configurations:
- Single plate with chevron pattern for parallel flow for optimum thermal performance and pressure drop.
- Single plate with chevron pattern for diagonal flow for optimum thermal performance when mounted horizontally and complete drainability is required.
- Double-wall plate when you need to avoid mixing fluids.
- Gemini double-wall plate when you need to avoid mixing fluids in hygienic applications.
The distribution area ensures that fluids are evenly distributed to the heat transfer area and helps avoid stagnant zones that may cause fouling.
There are a number of design features that help maximize heat transfer. The high efficiency per m2 minimizes the number of plates and the raw material used. This results in a compact, space-saving unit.
While high flow turbulence between plates results in higher heat transfer, the consequence is pressure drop. Our thermal design engineers can help you select the model and configure to what is suitable for your application so that it delivers maximum thermal performance with minimum pressure drop.
Gasket profile
Gasket glue
The gaskets are used to efficiently seal the heat exchanger. The gasket profile, width, thickness, type and compound of polymer are configured to each heat exchanger and its intended duty. Depending on application and frequency of unit openings, the gasket is either fastened by its clips or fingers or glued to the plate. We use a specially developed two-component cured epoxy glue for maximum adhesion in applications where frequent cleaning is necessary.
AHRI certified industrial gasketed plate heat exchangers
The Alfa Laval AlfaQ range of heat exchangers are certified according to the AHRI* Liquid to Liquid Heat Exchangers (LLHE) Certification Program (AHRI 400) which ensures thermal performance according to a manufacturer's published specifications. Typical HVAC applications include district cooling substations, ice-storage systems, data centre cooling and free cooling systems. To read more about the Alfa Laval AlfaQ range.
- Eliminate uncertainty about thermal performance
- Reduced system-wide energy use and operating costs
- Uncompromised environmental performance
- Independent assurance
- Three-year warranty
Under-dimensioned heat exchangers can lead to higher system-wide energy use, higher operating costs and compromised environmental performance. With AHRI certification, you are assured that the plate heat exchanger will function as required. No risk of underperformance. No uncertainty. It does what it says on the box, guaranteed.
*The US Air conditioning, Heating & Refrigeration Institute (AHRI) certification is the only global, third-party performance certification for plate heat exchangers.
Alfa Laval energy news on LinkedIn
Our showcase page with the solutions you need to stay ahead.
