Biopolymer production
Plastics are integral to our daily lives. Currently, over 500 million tonnes of plastics are consumed annually, with more than 98% derived from fossil carbon. To achieve Net Zero emissions by 2050, we must transition to 100% circular carbon sources by switching to circular feedstocks such as biocarbon, CO2 capture and recycled carbon. In the race to reach our collective sustainability goals, biopolymers are being used as a more circular solution to conventional petroleum plastics. While the technology has been available for over 100 years, bio-based plastic production has been growing in popularity due to recent global directives aimed at reducing single-use plastic. Additionally, there is growing concern about the environmental impact of microplastics and their effects on human health.
Alfa Laval empowers you to achieve:
- Boosted product recovery
- Optimized product purity
- Improved energy efficiency
- Sustainable water management
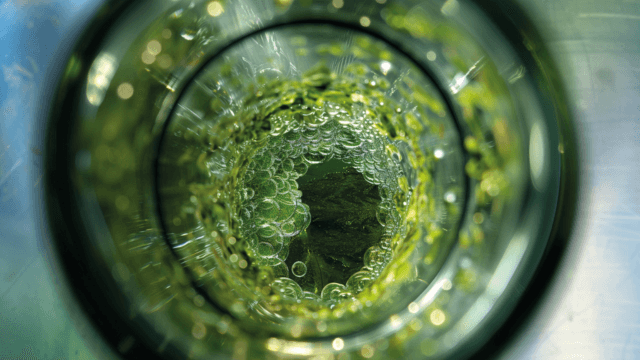
Circular polymers
Biopolymers, such as polyhydroxyalkanoates (PHA), polylactic acid (PLA), Polyethylene Furanoate (PEF), succinic acids, 1,3-propanediol (PDO), 1,4-butanediol (BDO) and 2,5-furandicarboxylic acid (FDCA) are polymeric materials produced from renewable biomass sources, often through industrial fermentation.
PHA
PHA is produced by fermenting natural raw material such as sugar or lipids. In this case, the fermentation is intracellular, which means that the fermentation product (PHA) is stored inside the microorganism body. In order to harvest the produced biopolymer, the bacteria cells need to be separated from the fermentation broth and afterwards lysed (by chemical or physical methods), and then PHA will be extracted from the cell debris and purified.
PLA
PLA bioplastic is produced by bacterial fermentation of sugars, but unlike PHA, the product of the fermentation, lactic acid, is excreted into the fermentation broth in what is called extracellular fermentation. The lactic acid will be further purified by evaporation and distillation and then polymerized to obtain the PLA bioplastic.
Products and solutions
Separation technology
Increase your separation efficiency and reduce energy consumption in completely enclosed operation.
Disc-stack separators play a crucial role in biopolymer production. When there is a need to separate liquids with a lower concentration of solids and smaller particle sizes, centrifugal force can be used to get a more effective result. Disc-stack separators are used in the main production process to separate the biopolymer from the fermentation broth and are also utilized in downstream washing steps, concentrating the biopolymer while removing impurities such as cellular debris and excess water.
Increase your separation efficiency and reduce energy consumption in completely enclosed operation
With the help of Alfa Laval’s patented hermetic design, the bacteria will not break before the harvesting phase. Our unique design is specified to this type of process, guaranteeing a more efficient, higher yield with 40% less power used. This design can be found in both PLA and PHA production, depending on if you are using our Clara or PurePulp centrifugal separators.
Heat transfer
Plate Heat Exchangers for heating and cooling applications, such as sterilizing or fermenters cooling.
Alfa Laval heat exchangers are top-tier technology designed to optimize heat transfer across various industries. Their compact design, flexibility, easy maintenance, and high efficiency make them the ideal solution for heat transfer applications. In biomanufacturing, these heat exchangers enhance process control and energy efficiency, ensuring consistent product quality and reducing operational costs.
Water management
Optimized water recovery for reuse
Biopolymer production requires a substantial amount of water due to several washing stages. Normally this water is managed in a regular wastewater treatment system, but with the help of Alfa Laval’s zero liquid discharge technology, this water doesn’t have to go to waste. Instead, it can be cleaned, recycled, and reused to improve production efficiency and your carbon footprint. Our water and waste treatment solutions will reduce your carbon footprint from wastewater streams. Plus, we have years of expert experience in separation and thermal technologies for these types of applications.